株式会社 建和のコンサルティング事例
本号で紹介プレスメーカーは、以前登場した株式会社 建和(愛知県安城市 TEL 0566-92-6295)である。同社は、自動車部品において60tプレスから300tまでのプレス量産加工を行い、最新のサーボプレスも有効に活用している。
同社で発生している問題とその発生原因
440Mpaから980Mpaといったハイテン材を扱う同社では、特にショット数の多い順送型などにおいて、メンテナンス頻度が従来よりも多く発生しているという問題が生じている。
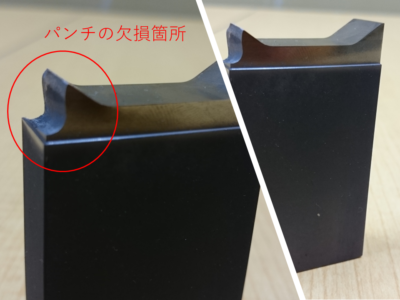
特に、社内で設計製作した金型よりも、協力メーカーの金型メーカーに設計製作を依頼した金型に多く問題が発生していた。
その原因の一つとして、プレスメーカーにて1万、10万ショット以上打った後の金型の状態を、金型メーカーが詳細に把握できておらず、必要な強度で金型を設計できていないためだと筆者は考えている。
金型メーカーでは、どこまでの強度の構造を持つ金型を設計すればよいか、どれだけの強度の金型材料を用いればよいか、考慮することが難しくなっていると考えられる。
また昨今は、金型にかけられる予算が限られており、厳しいコストで金型製作をしなくてはならないため、金型メーカーとしても過剰な品質の設計は避けたいところである。
とはいえ、金型メーカーの力量が劣ってきたとか低下しているということではなく、590Mpaを超えるハイテン材の順送プレスなど、大ロットのプレス加工において、未知なることがまだまだ多く、金型メーカーとしても情報を蓄えきれていないのが実情なのだと筆者は考えている。
具体的な問題事例
同社で発生している金型破損・故障の多くは、①応力集中・座屈、②金型材料の選定、に起因している。
例えば、応力集中を起因とする破損例として、抜きや曲げのパンチに多く発生している。
応力集中とは、パンチなどにある凹形状部において、ピン角やごく小さな凹R形状があると、プレス加工時にかかる負荷により、パンチにかかってくる荷重が分散されず、そのピン角部や小さなR部に集中して負荷がかかってくる現象である。
これにより、強度計算上、折れない太さ・長さのパンチであっても、応力集中がかかってくる部位で破損してしまう確率が非常に高くなってしまう。
こういった形状を持つパンチは、協力メーカーで製作された金型に多かった。この傾向は現場経験のある筆者もよく理解できるが、角部にわざわざ大きな凹Rをつけるためには、エクエアエンドミル加工にくわえ、ボールエンドミル加工も追加する手間が発生する。もしくは大きなR形状を持つラジアスエンドミルを使わなくてならず、加工形状によっては使えない場合も発生する。
さらに、せっかく5Rなど応力集中を緩和するための適切な大きさを持つ凹R部を、ボールエンドミルを使って加工しても、先行して加工しているスクエアエンドミルとの境界部に微小なピン角が残っているため、そこから破損しているという事例もみられた。
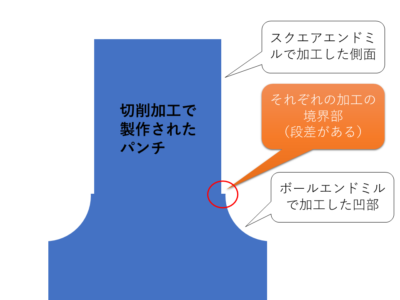
またせっかくボールエンドミルにより、大きな凹R形状が加工されていても、その切削加工面が粗いと、その粗い面の凹凸が微小な凹形状となってしまい、そこへの応力集中によって破損が発生することもある。
もう一つ、②の金型材料の選定による故障も発生していた。
例えば、抜き加工を行う金型において、パンチを保持するパンチプレートの材料について、安価なSS400を使って製作する金型メーカーは多いが、1万ショットを超える量産に使った金型をメンテナンスのため分解すると、パンチを保持するインロー部がグラグラになってしまった状態をよく見かける。
これについては、ハイテン材ではない普通材や、薄板の小ロット生産であれば問題ないかもしれないが、ハイテン材や厚板の順送プレス加工においては、最低でもS50Cや焼入れ処理した硬いプレートを使わないと、前述したようなグラグラな、きちんと保持できない状態になってしまい、抜き加工時に発生する衝撃により一気にパンチの摩耗・破損が進んでしまう。
パンチの下にあるバッキングプレートに焼入れが入っておらず、やはりSS400が使われている金型も多く見かけるが、ハイテン材をプレスする金型においては、SK105を焼入れしたプレートを使うか、パンチの下に焼入れ処理した入れ子プレートを入れるなどの対応をとりたいところである。
こうしたハイテン材などの難加工材を扱ううえでの諸問題のデータベースは、今現在、金型メーカーよりもプレスメーカーの方に多く蓄えられており、プレスメーカーにとってこれは大きな財産であると言える。
プロジェクトの立ち上げとコンサルティングの取り組み内容
そこで、代表取締役である山本道典氏は「壊れない金型づくり」をテーマに、プロジェクトとして立ち上げ、筆者と共に、自社で扱う金型を根本的に見直していく取り組みを行った。
具体的な取り組みステップは、次のとおりである。
- 基礎学習
- 実践応用
まずは、設計と製造の主要スタッフが、金型に要求される強度や、金型が壊れるメカニズムなどの基礎知識を持つための研修を行うことから始めた。
例えば、金型で使われる主要パーツの強度はどのように計算するべきか、金型材料の特性の違いはどのようなことがあるのかなどを学習した。
実践応用のステップでは、実際に破損した金型やプレス製品を事例として取り上げ、学習した基礎知識と照らし合わせ、そもそも必要であった金型要件からどのようなギャップがあったのかという視点から原因を調査した。
とかく金型修理については、長時間プレス生産を止めることができないことから、早急な応急処置対策を取ることが多くなるが、本来あるべき金型構造・金型強度とのギャップ分析から金型改修を行うべきである。
そのためには、金型設計者だけではなく、保全に関わる者も、金型構造・金型強度に関する基礎知識を持っておくべきと筆者は考えている。
コンサルティングの効果と同社の今後の取り組み
今回のプロジェクトにより、同社の金型改修は、応急対策・恒久対策を切り分け、計画的に進めていく体制を作ることができ、今現在、筆者と共に着手している。
今後の同社の取り組みとして、前回登場の際、書かせていただいたように、以前はアウトソースしていた金型製作を3年前より内製化できる体制を構築しており、解析技術や全工程の3次元データ活用、自動スケジューラーなど、積極的に最新技術を導入している。
その最新技術の進化形である次なる取り組みとして、3次元設計の自動化・高効率化や、プレス解析の最適化技術などの活用も、大学やITベンダとも連携しながら進めている。
最新技術の導入に加え、プレスメーカーとして日々蓄えている実績・経験のビックデータを、ハイテン材プレス金型の質向上という形で新たな強みとし受注競争力UPを図っている。
ソフトウェアの最新技術のみならず、技術者の基礎・応用能力UPとの両面で、同業他社との競争力向上を図っている同社に、筆者は大きな期待をしている。
金型・部品加工業専門コンサルティングからのご案内
ホームページの技術コラム本の第6巻が発売されました!
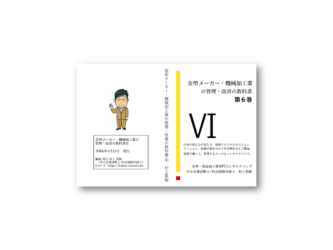
設計部署や製造現場、管理部署にぜひ一冊。
経営者や部長などマネージャー職の方々から、悩める現場リーダーへのプレゼントにも最適です。
くわしくはこちらのページからどうぞ。
【改善・管理の上級編】セミナー動画が発売中です【お得なDL版あります】
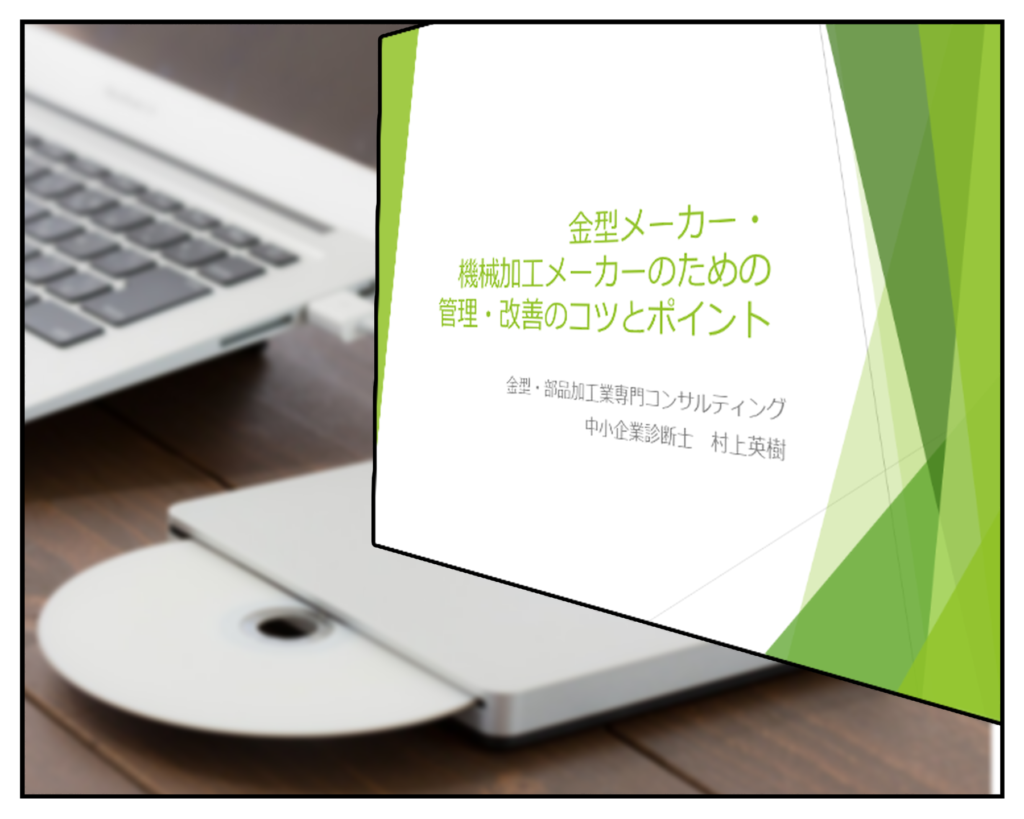
過去に大手セミナー会場で、代表コンサルタントが講師として登壇した内容をZOOMで再収録しました。
内容は、加工や管理における上級コースとなります(基礎知識はすでに持っておられる方向けになります)
動画セミナーですので、いつでも何人でも受講でき、長時間一気に受講する必要もありません。隙間時間を有効に使って受講できます。
お買い求めしやすいダウンロード版もございます。
くわしくはこちらのページからどうぞ。
【書籍販売中です】経営が厳しい金型メーカーのための本
このホームページに掲載している多くの技術・管理コラムから、経営が厳しい金型メーカーのために、大きな投資に頼らず、意識面や仕事の取り組み方などから改善改革していける方策に関するコラムを集めた本をつくりました。
こちらの書籍を販売しております。内容は、366ページの大ボリュームとなっております。
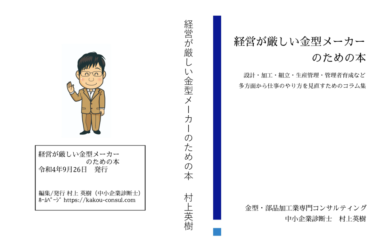
ぜひ社員の皆さまで読んでいただければと思います。また、金型メーカーを支援される金融機関や公的機関、会計事務所やコンサル会社でお勤めの方々にも、読んでいただければ幸いです。
詳しくはこちらのページからどうぞ。
YouTubeを使った上級セミナーを配信中です
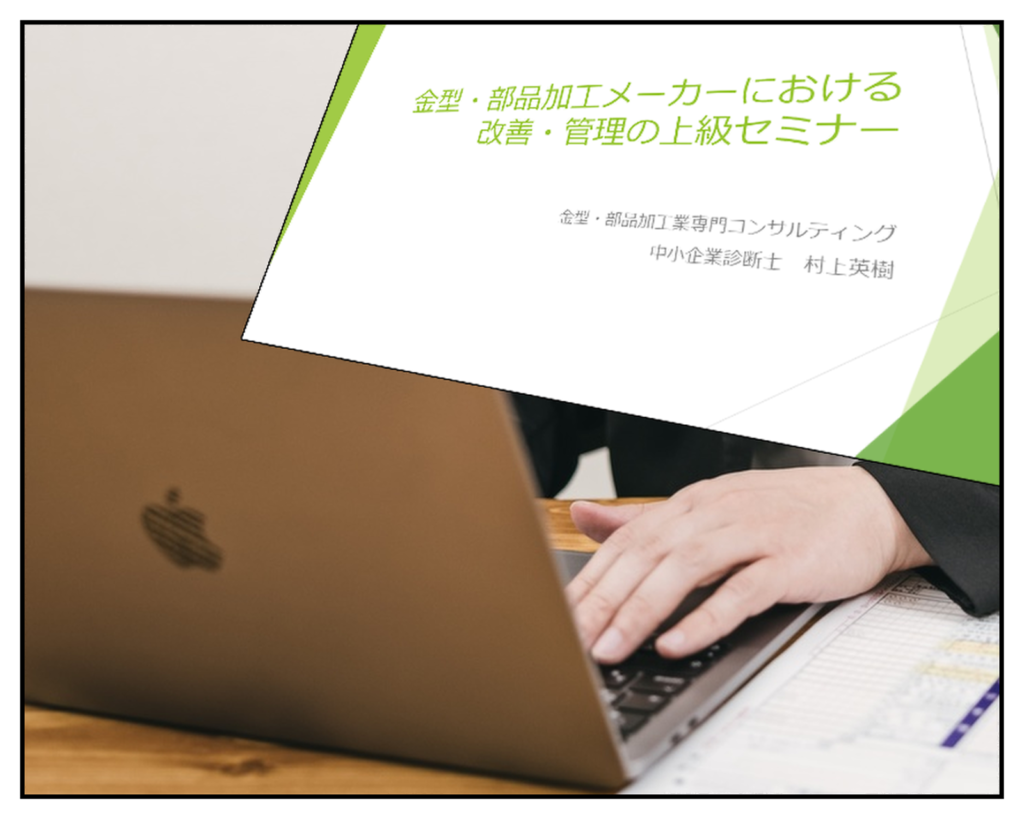
金型メーカー・部品加工メーカーにおける、個別テーマの上級セミナーを配信しております。
YouTubeによる動画配信ですので、ネット環境があればいつでもどこでも視聴できます。
くわしくはこちらのページからどうぞ。
「金型メーカー・機械加工業のための管理職育成マニュアル」発売中です
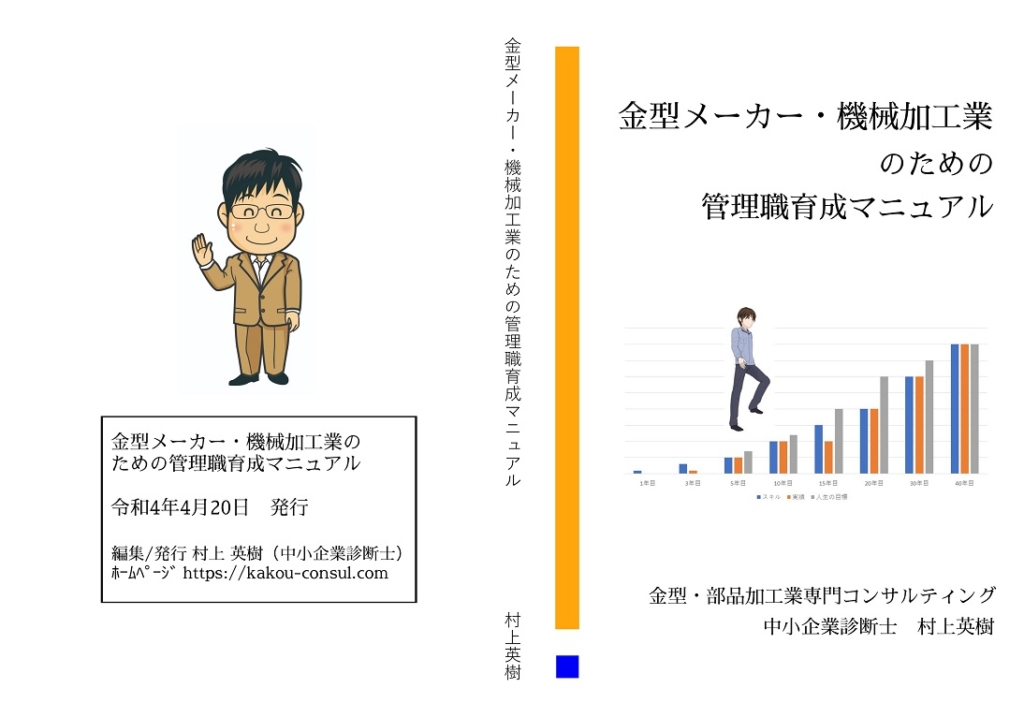
当サイトの管理職育成ルームに掲載しているコラムを集めて編集したものになります。
金型メーカーや機械加工メーカーで、新たに管理職になられる方や、すでに管理職としてお仕事をされている方向けに、ストーリー形式で、心構えから具体的に取り組む業務内容まで、幅広くまとめております。
くわしくは、こちらのページからどうぞ。
「金型メーカー・部品加工メーカーにおける処世術」が発売中です
こちらの書籍は、金型メーカーや部品加工メーカーにおいて、国内全体で賃上げの機運が高まる中、勤める会社に貢献しながらも、ご自身の付加価値・市場価値を高めていこうとされる方々の一助になるような内容をお届けすることを目的としています。
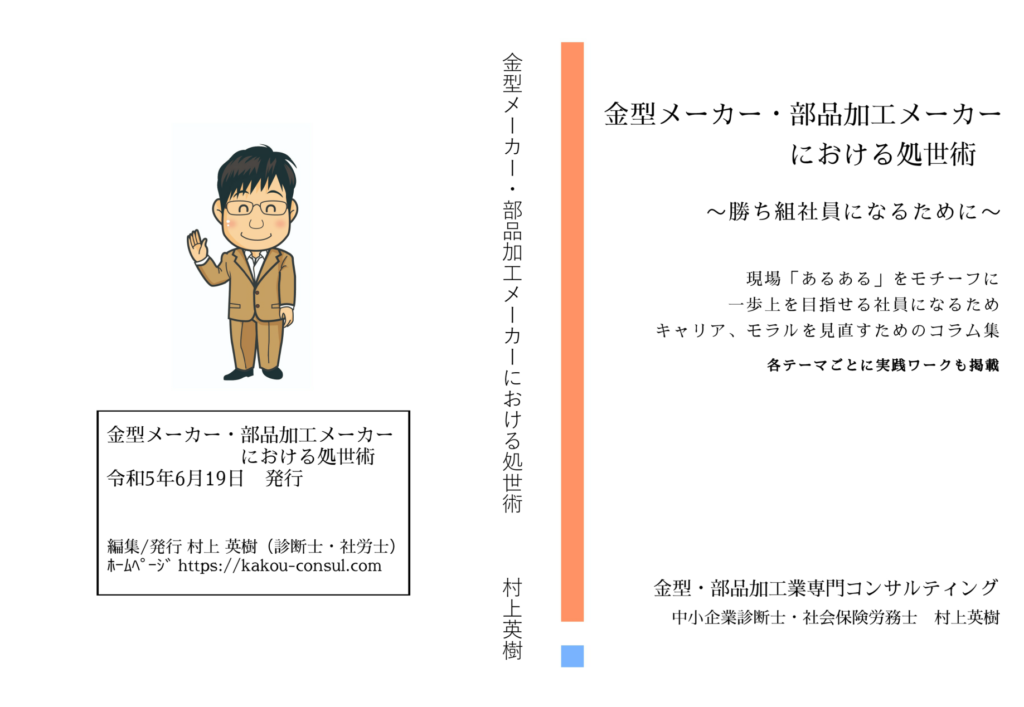
「処世術」をテーマにした一般書籍はたくさんありますが、主にホワイトカラー向けのものが多く、金型メーカーや部品加工メーカーのお仕事ですぐに使えるものが少ないと思っています。
一方この本では、金型メーカーや部品加工メーカーの現場「あるある」を題材にしており、そこでお仕事をされる方々に身近なわかりやすい内容にしております。
簡単なワークも掲載していますので、社内研修にもお使いいただけます。
詳しくはこちらのページからどうぞ。
「金型メーカー・機械加工業のための自己診断ハンドブック」が発売されました!
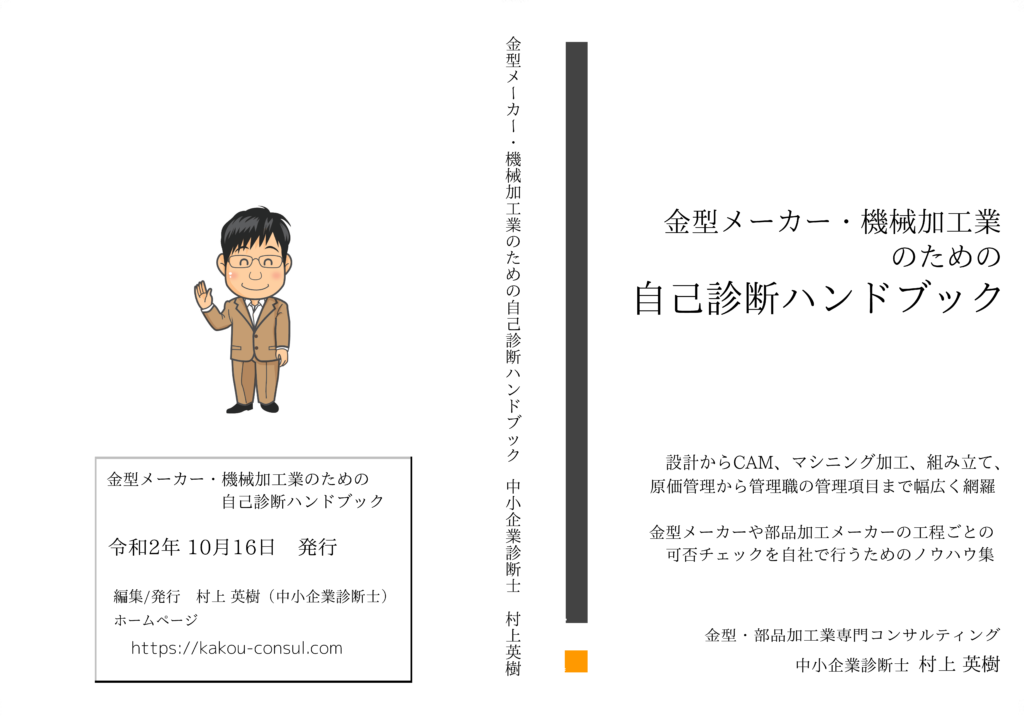
私がコンサルティングの初回訪問時や、無料診断サービスにおいて、訪問先企業の製造現場で確認する項目を解析付きで紹介しています。
金型メーカーや部品加工メーカーに皆さまに、自社をセルフチェック(自己診断)するために使っていただければと思っております。
くわしくはこちらのページからどうぞ。
2パターンの技術セミナーレジュメを販売いたします
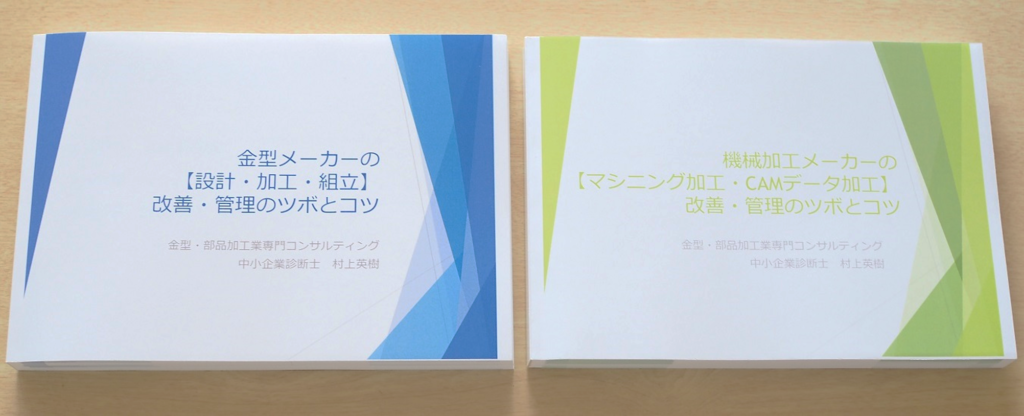
日刊工業新聞社さん主催で行われた、機械加工メーカー向け、金型メーカー向け、それぞれの技術セミナーで配布されたレジュメを販売いたします。どうしても遠方で参加できないといった方や会社さまより、レジュメだけでも使いたいとリクエストがあったためです。
当事務所のホームページに掲載されているコラムの内容がベースとなっておりますが、それとの違いとしては、具体的計算と事例ワークなどを盛り込み、ホームページよりも手厚く解説しております。
本来レジュメと言いますと、図やイラストがほとんどで、言葉による文章が入っていないイメージがありますが、本レジュメはそうではなく、復習がしやすいよう、多くが文章で構成されており、1人で読み進めることができます。
くわしくはこちらのページからどうぞ
ミドルマネジメント層向け人材育成セミナーのレジュメを販売いたします
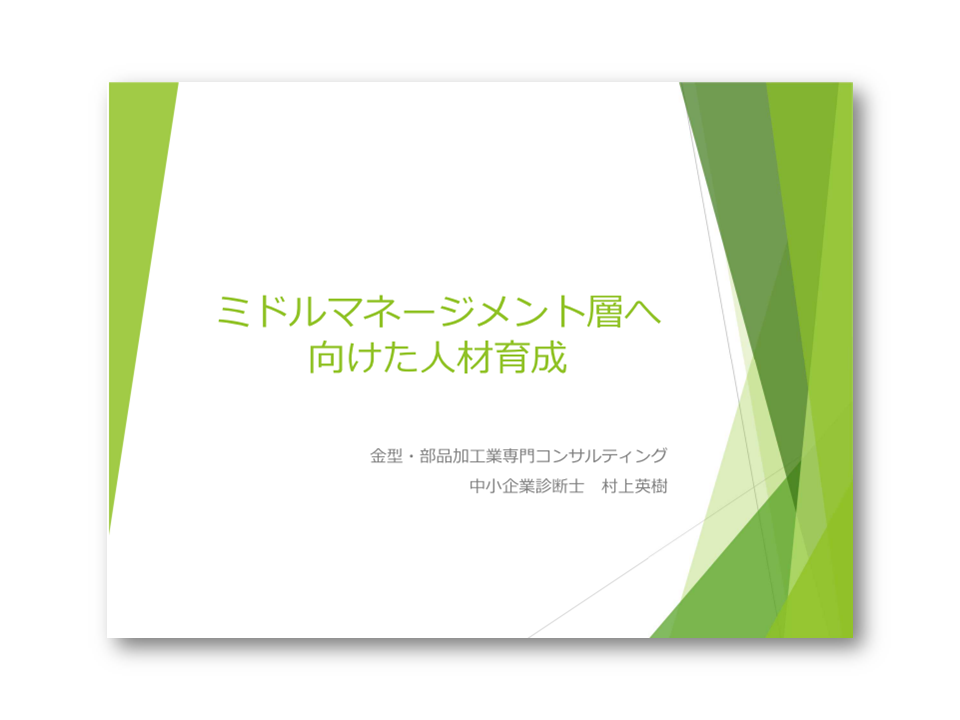
ミドルマネジメントの人材育成のテーマで、講演をさせていただいた際に作成したレジュメ(当日映写したパワーポイントファイルと同じものです)を販売いたします。
日程や生産管理、品質管理だけが幹部・管理職の仕事ではありません。儲けるためのマネジメントが必要です。
そういった視点や意識を持ってもらうためのきっかけとしてオススメの一冊です。
くわしくはこちらのページからどうぞ。
4コマ漫画ギャラリーを開設しました
コラムページにプロローグとして添付している4コマ漫画を集めたページを開設しました。
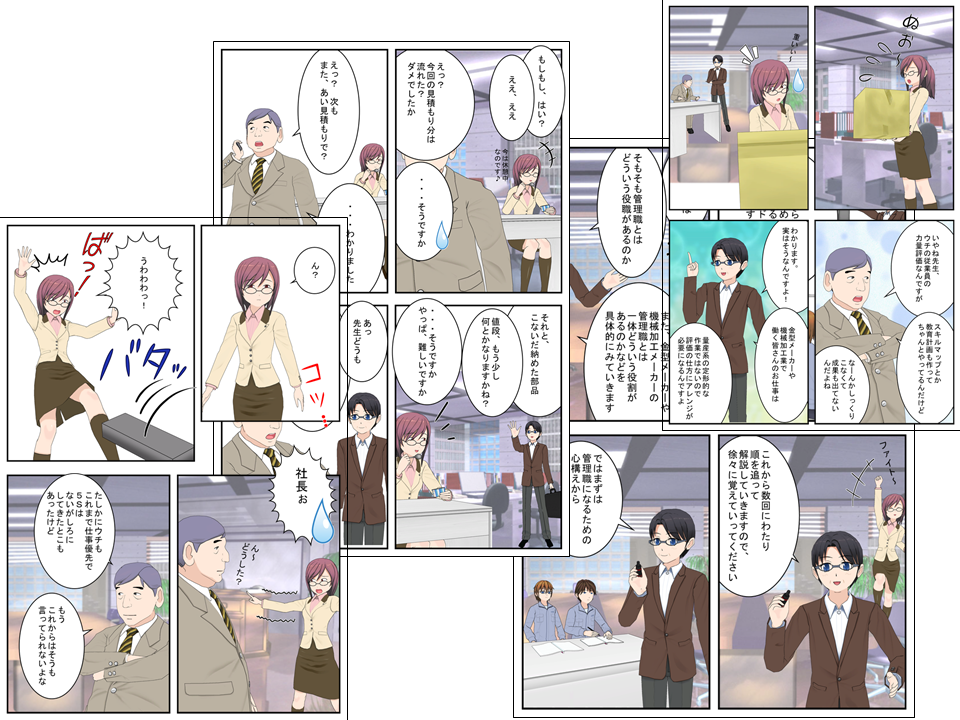
こちらをクリックすると入れます

コラム投稿者
金型・部品加工業 専門コンサルティング
代表:村上 英樹(中小企業診断士)
愛知県刈谷市 TEL 0566-21-2054